If you want efficient plants for turning municipal, commercial and industrial waste into fuel, you first have to define the end product. Especially in the single-stage production of fluidised bed fractions for thermal processing in cement-kilns / calciners , it is vital that the shredding systems work, for the most part, extremely robustly and reliably around the clock – since one single shredder turns waste into a precious, defined fuel that one is more than entitled to call a ‘product’.
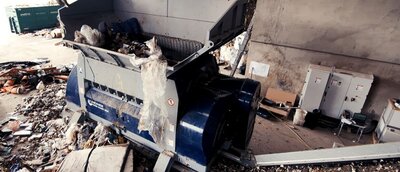
Economic Production Of Alternative - Fuels For Calciner Firing
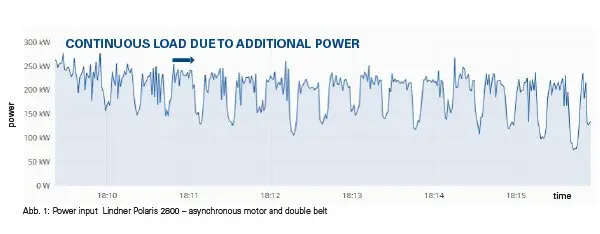
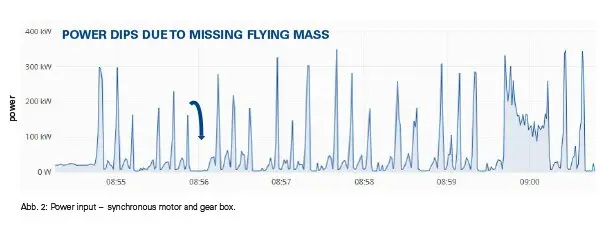
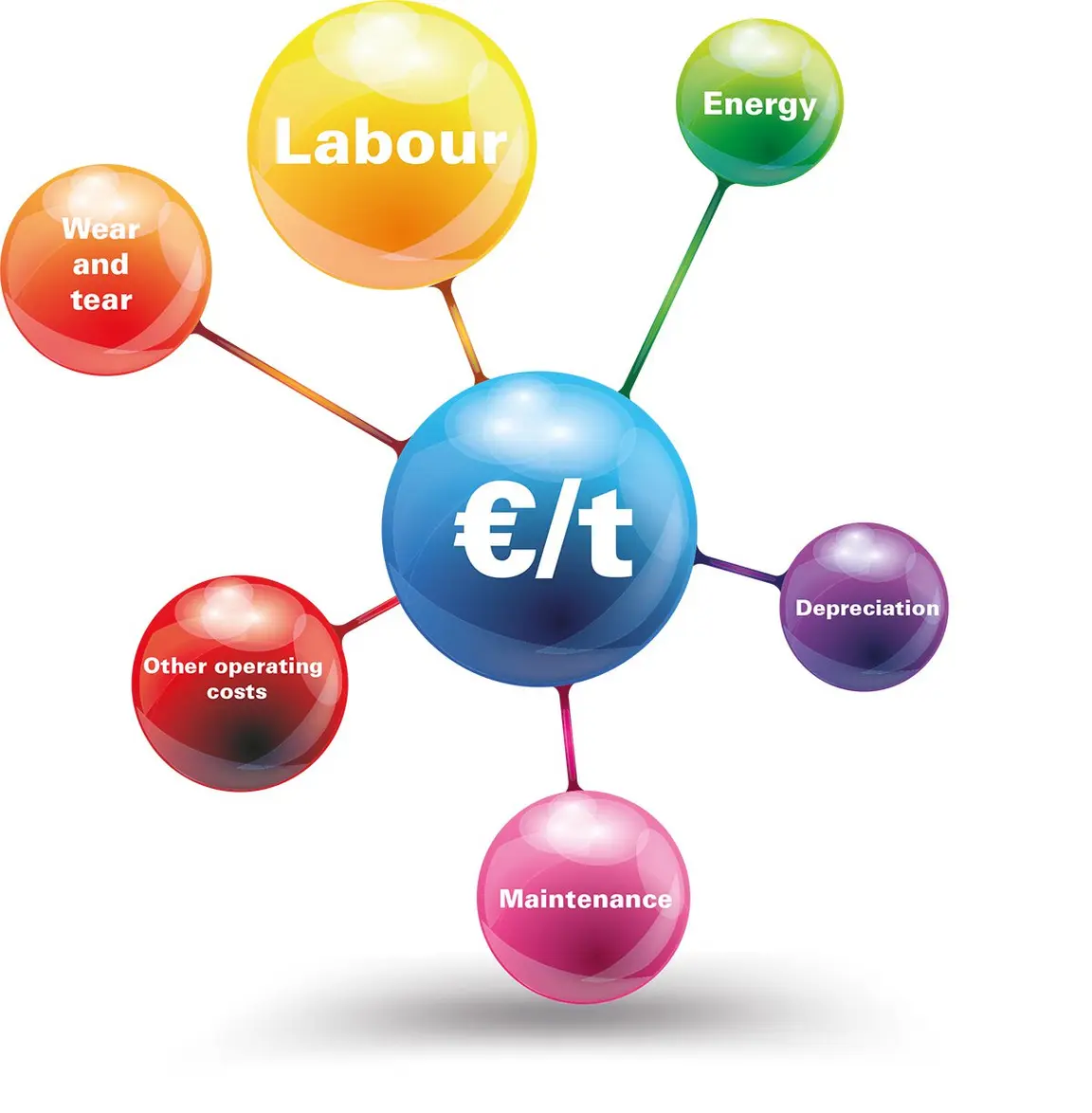
If you look closely at the profitability of the system, the shredder – as an almost standalone solution for this type of processing – becomes the centre of attention. Not only is a great amount of RDF produced during the machine’s lifetime, but costs are also accumulated. In addition to the proportional acquisition costs, wear and tear as well as energy and labour costs have to be considered. These directly influence the system’s profitability. If you total and divide these costs by the amount of the final product produced, you get the costs per ton (€/t). This figure is extremely important when judging the machine’s profitability.
Examining these costs further, you realise that it is all about time. The costs per operating hour are directly related to the productivity i.e. the throughput per hour. Crucial are labour costs, machine downtime and, to a lesser extent, other factors that generate costs, such as the operating hours for additional equipment (loaders, belt conveyors etc.).
To get a more realistic picture, Lindner commissioned a series of tests with two different shredding solutions at the prestigious Department of Environmental and Energy Process Engineering of the Montanuniversitaet in Leoben, Austria in May 2017. The University tested under standard conditions the single-stage process of turning different types of waste into fluidised bed fractions.
They focused on typical untreated waste from commercial and industrial sectors and used a Lindner Polaris 2800 with a 2 x 132 kW, as a representative for the double belt drive and the asynchronous motor, as well as another regarding price and size comparable market solution with a 2 x 113 kW synchronous motor and gear box.
It is remarkable that, depending on the selected material, the Lindner machine with its merely 20% higher connected load was able to produce an hourly output that was up to 2 times higher than the other machine.
To understand this result better, we have to check the input power of the two shredders over a certain period of time. Untreated waste, in particular, often contains materials that are more difficult to process. This means that often the required power would be higher over a short period of time and the double belt drive can show all of its power. The double belt drive works just like an excessively large flying mass that functions as a rechargeable battery. If the shredder in operation is not fully utilised, the mass charges itself and is then able to compensate when load peaks occur. Thanks to this excess power the machine can continually shred even difficult material with a high throughput.
In contrast, the other machine had an extremely irregular power input with frequent power dips. As it lacks the excess power generated by the double belt drive, this machine experiences power dips and almost stops working altogether sometimes, especially when shredding tough materials. Precious minutes are lost when the cutting rotor has to start anew or reverse. In total this means a lower throughput per hour. As was demonstrated by the practical test, with the double belt drive the machine can produce up to bouble the amount compared to the other machine in the same time.
Moreover the combined synchronous motor and gear box without any excess power from the double belt drive often reach their performance limits. For the profitability of the system this higher and irregular load means that the singular machine components are put under more stress. This in turn can negatively impact the life, wear and tear and therefore profitability of the system in the long run.
So if we summarise the results, it becomes quite clear which one of the two machines is the more profitable investment.