Spittal an der Drau/Austria & Großbottwar/Germany, August 2021. Changing from a linear to a circular economy, the quality of the recycled material plays an increasingly important role. Lindner, one of the leading manufacturers of shredders, system solutions and industrial washing systems for plastics recycling, is taking on this challenge and will be presenting a new hot-wash system for recovering PET (polyethylene terephthalate) at Fakuma 2021, booth A6-6108. Equipped with the new hot-wash tower and the also new Lindner step dryer, the company is setting new standards in PET recycling. Lindner Recyclingtech's Micromat shredder series deliberately focuses on quality, reliability, robustness and experience.
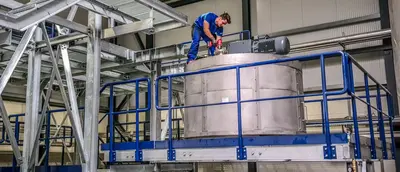
The New PET Hot-Wash System and the Micromat Premium Shredder
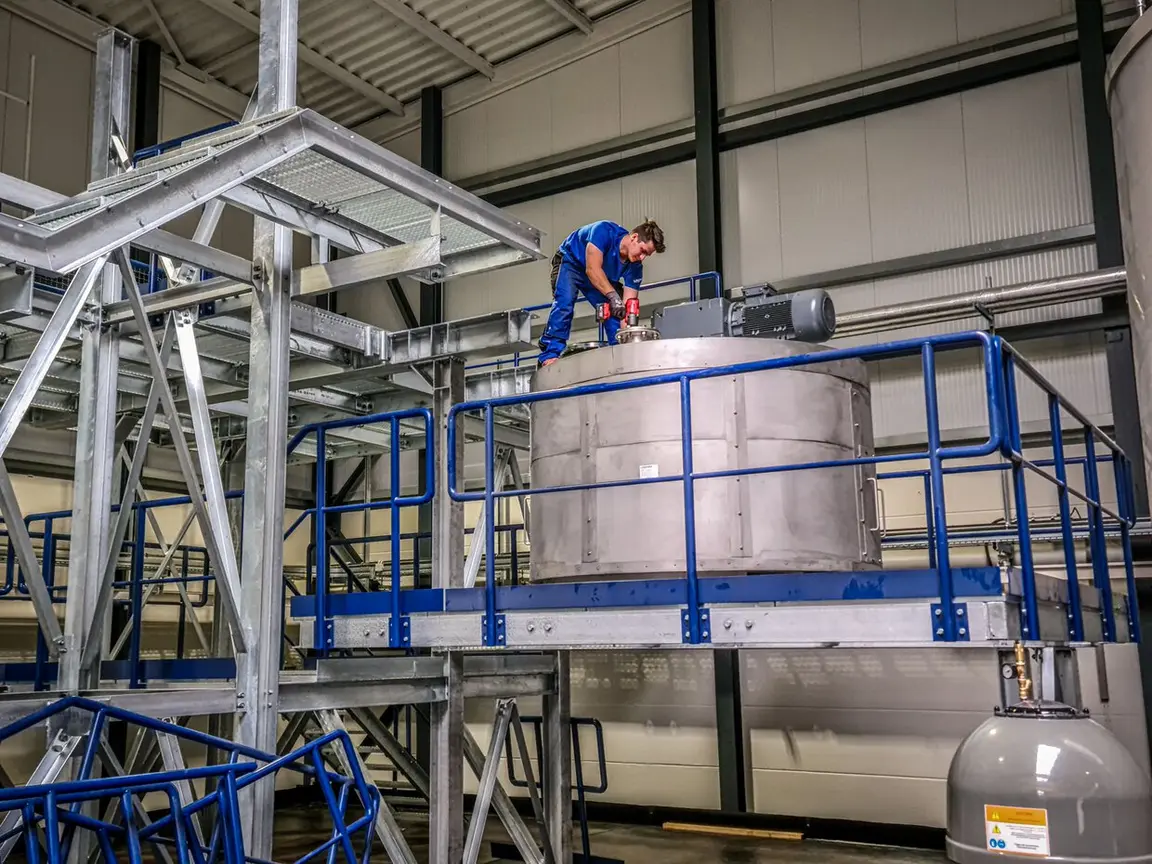
Lindner’s new PET hot-wash tower for high-quality PET recycling
The circular economy remains a hot topic. Sustainability, resource conservation and the reduction of the ecological footprint take centre stage and underline the necessity of recycling all kinds of plastics. In addition to efficiency and cost-effectiveness, the main challenge is to use a reliably functioning system that allows for a high degree of flake purity and therefore high-quality recyclate.
Lindner Recyclingtech’s original powerhouse, the Micromat, shreds waste materials reliably and efficiently. The signature feature of the Micromat series is its Mono Fix rotor, which guarantees universal applicability by enabling different or mixed rotor configurations. Various pointed or flat knives and special counter knives can be fitted to one and the same rotor as required depending on the input material. As a result, this Mono Fix technology ensures a high and consistent throughput with a wide range of materials that are often classified as difficult.
New at Lindner Washtech
The latest product from Lindner's subsidiary Washtech is the hot-wash system with the PET hot-wash tower and Lindner’s step dryer, which were developed specifically for the PET sector. The innovative stainless steel step dryer dries the material particularly gently by slowly adjusting the rotation speed in five steps. This results in less friction and a lower fines content. The compact step dryer delivers throughputs of 1,000 – 3,000 kilograms per hour at a drive power of 30 kW.
Thanks to the new hot wash, the last remaining contaminants such as adhesives, labels and prints are reliably removed from PET bottles. The PET hot-wash tower can be operated with or without caustic solution and works with a separate water circuit. Gentle cleaning and defined dwell times guarantee high-quality output materials, which are the perfect basis for producing food grade rPET.
The first PET line with the new components has already been sold in German-speaking countries, and commissioning will take place this autumn,’ says a delighted Harald Hoffmann, Managing Director at Lindner Washtech. Lindner Washtech supplies the turnkey line including NIR sorting, label remover and water treatment. ‘With our new washing components, we also want to set new standards in the PET sector and make an important contribution to a functioning circular economy,’ Hoffmann emphasises.
Lindner at Fakuma 2021: Booth A6-618

Lindner Recyclingtech's original powerhouse: The Micromat Series